“My boss tells me to keep the rollers on my 125X gyratory compactor clean. Does it really matter?”
Yes, it really does matter.
Do the rollers on your machine look something like the ones below? If so, you’ve got your work cut out.

Understanding the System
First, let’s get on the same page with correct terminology. The term “rollers” is widely used with respect to the 125X, but the correct term is “cam followers” which is what we will use in the remainder of the article.
Understanding the function of the cam followers on the machine will help you see why having cam followers like the ones pictured above is bad—bad for your costs and bad for your test results.
Figure 2 provides a view into the compaction chamber of a 125X. There are three sets of three cam followers, two horizontal and one vertical (Figure 3), located on three vertical links. The left link is called the adjustable link. The machine lifts this link to impart the angle of gyration. The center link is the intermediate link. The right link is the fixed link. It is fixed to the base. The links are connected into a system called the carriage.
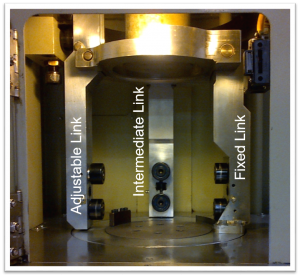
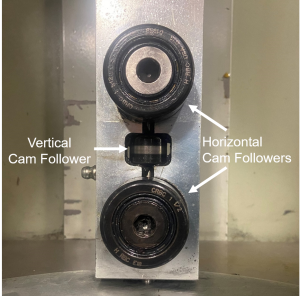
A prepared mold (Figure 4) properly placed in the compaction chamber has the mold flange situated between the horizontal cam followers on each link. The machine raises the adjustable link, which lifts the left side of the mold. The fixed link on the right is attached to the carriage base in a fixed position. The raising of the adjustable link imparts the angle of gyration to the mold. The angle of gyration imparted, the carriage rotates to cause the gyrating action.
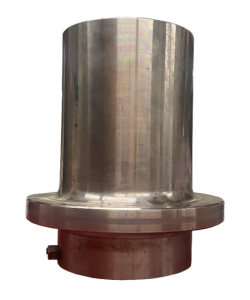
The vertical cam followers serve the purpose of conveying the mold flange past the link with limited resistance. The lack of a vertical cam follower would cause friction between the face of each link and the face of the mold flange.
Potential Problems
Properly positioned horizontal cam followers have a specified gap between them that is designed to allow the cam followers to pass freely over the flange while applying a consistent angle of gyration to the asphalt mixture during compaction. As asphalt accumulates on the cam followers, the gap between the cam followers gets smaller. Two things can happen as the gap narrows. (1) The cam followers can pinch tight on the mold flange causing the mold to rotate with the carriage. (2) The force applied on the cam followers as the flange passes through them widens the gap by wearing the cam follower (Figure 5) or moving the position of the cam follower. Both cause problems.
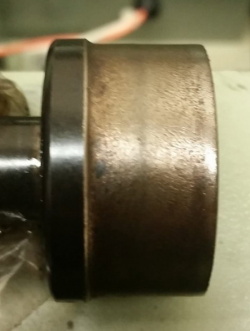
An extreme buildup of asphalt on the vertical cam followers could result in the cam followers becoming stuck and the carriage grabbing the mold and trying to rotate it.
The Mold Rotates with the Carriage: Early Superpave requirements allowed the mold to rotate twice in 200 gyrations. The 125X system is designed to allow a mold to make a maximum of one full turn during the compaction of a specimen regardless of the number of gyrations. An anti-rotation cog mounted beneath the mold flange is positioned to engage an anti-rotation cog on the carriage base to prevent the mold from rotating (Figure 6). If the mold begins to spin with the carriage system, the cog on the mold will strike the cog on the base and prevent the mold from rotating. Repeated impacts and the force required for the anti-rotation cog system to keep the mold from spinning can result in broken cogs and/or broken cog screws that can be expensive to repair. Also, if the cog system stops the rotation of the mold and the mold doesn’t break free from the cam followers, the base motor will stall.
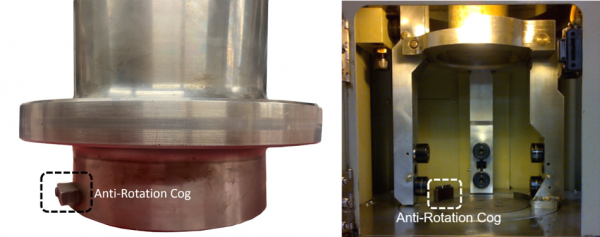
Widening of the Roller Gap: The cam follower gap is set during calibration so that the machine compacts asphalt mix at the specified internal angle of gyration. A larger-than-intended gap between the cam followers leads to a lower angle of gyration. A lower angle of gyration results in specimens of lower density, which may cause problems.
What does Pine recommend?
- If your cam followers are dirty, clean them. Remove loose debris. Saturate with WD40 and allow it to soak. Then, use a scraper to remove the asphalt binder. Several cycles of applying WD40, soaking, and scraping to completely remove binder from the cam followers may be required.
- Remove all asphalt binder from the mold flange using WD40.
- Once your cam followers are clean, keep them that way. Wipe them clean after each use. Some WD40 and a rag will do.
- Keep cam followers from getting dirty by wiping clean the mold flange each time you fill the mold with asphalt and before you place the mold in the machine. WD40 will loosen asphalt binder, help prevent the mold from rusting, and lubricate the flange/cam follower interface.
Want to Learn More?
Click here to view a video on how to properly lubricate your 125X gyratory compactor.
Visit our website or talk with one of our specialists at 724-458-6393.